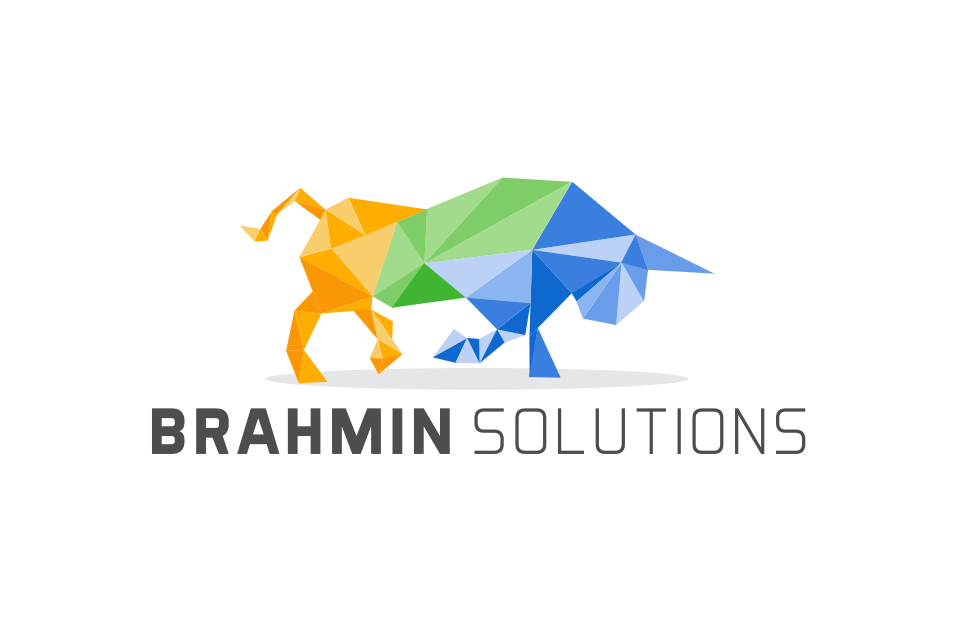
Manufacturing and Inventory Management Software
What happens when you find something you like and you place an order?
Then you end up waiting for it a lot longer than you expected.
That is lead time. Lead time is the time between when you order something and when it arrives. Knowing this for inventory management and supply chain planning is very important.
Want to learn how to calculate it?
Don't worry, this won't be like math class in high school again!
In this article, you’ll learn about the lead time, the lead time formula, and the easiest way to track it. Let's get started!
Lead time is the time it takes for one work unit to go from the beginning of the production and delivery cycle to the end. For example, for a manufacturer, the lead time is the period when a manufacturing order comes in and until the time it's completed.
But why should you bother calculating this metric?
To answer this, we need to dig a little further into the world of inventory management or inventory control.
For example, let’s imagine you are a beverage manufacturer, and the process of producing them takes place in three steps:
Each of these steps takes some time. But what about the time between these steps? This is considered when figuring out how long it will take to make your product.
Lead time also considers the time spent making the purchase and the time spent waiting for materials.
These unsold products and unused raw materials are your inventory.
While managing it, you’ll need to be mindful of two things:
Before we explore lead times in more detail, let's take a quick look at another term people often confuse lead time with - cycle time.
These are words that can mean different things. When we talk about lead time versus cycle time, it usually comes down to when the clock starts ticking.
So essentially, your cycle time referred to as the order fulfillment cycle, doesn’t consider the purchasing process.
Although that metric is necessary, the focus should always be on manufacturing lead time.
At the end of the day, this is what the customer feels. They feel impatient when waiting. They want their delivery to be quick so that they can sell their products to customers.
It could be hours, days, or even weeks. This depends on how you usually do things.
But essentially, when figuring out how to calculate your manufacturing lead time (MLT), this is the formula you’ll be using:
MLT = Planning and Purchase Orders Made + Wait/Delay times + Materials received + Operations + Manufacturing completion
This lays the foundation you need to start increasing your efficiency and reduce that lead time.
Understanding the concept is crucial if you want to take advantage of it.
There are two steps to consider:
Planning lead time is the planning stage. This is when your purchase orders go out, and no work has started.
Processing lead time is the amount of time it takes to manufacture or get the item. So, to sum up, it includes:
Let's go back to the beverage manufacturer example.
The planning stage is spent on determining what raw materials are needed, sending out purchase orders, and planning the operations such as blending and bottling to make the product.
The processing stage is the actual production of the beverages.
You can use the formula above to figure out how much time each process and step takes to finish. This will help give you an idea of your manufacturing lead time.
The strength of a supply chain sometimes is in its simplicity. If there are many moving parts and more chances of failure, the weaker it becomes.
A short supply chain benefits everyone.
It benefits manufacturers, wholesalers, and retailers.
And most importantly, the end customer gets what they need when needed.
Understanding it is very important and we will go through an example of what happens if you don’t understand lead times.
If you are a retailer and you order a product with a lead time of one month and two weeks after placing the order, you research whether or not there is still interest in the product. If there is no longer any interest, the product that arrives in two weeks might become dead stock.
This is just a simple example of how things work for manufacturers who have to consider different types of lead times: material lead time, production lead time, and cumulative lead time.
If you have any delays in these lead times, it affects your overall manufacturing lead time.
This means customers' orders will be delayed and they will become unhappy. This will cause them to stop buying from you.
Reducing your manufacturing lead times as much as possible will help you avoid creating bottlenecks. Bottlenecks happen when you are waiting for deliveries or resolving customer wait times quickly.
So, how exactly can you go about reducing your manufacturing lead time?
A reorder point is when you order or manufacture more items based on how much stock you have on hand. Setting reorder points and keeping safety stock will help you stay in control of your inventory. This is important because it will help you stay lean and efficient.
Your safety stock is a buffer that helps you continue to fulfill orders even when there is a change in consumer demand or production delay. This is usually practiced by businesses that use just-in-time inventory, but it is a good practice for any business.
What makes a company good at inventory control?
It is being able to adjust and adapt.
So, producing products in small batches instead of large batches more frequently will make it easier to calculate safety stock levels and update reorder points accordingly.
Lean manufacturing principles say that it's helpful to place small orders frequently. There are a few benefits to this:
Inventory control sometimes hinges on good relationships.
Your relationship with your vendors will be significant in deciding how long it will take for you to get new raw materials. You can use incentives to ensure that the vendors get the items to you as quickly as possible. These incentives can be positive (like profit-sharing or priority status) or negative (penalties or loss of business).
This will encourage your supplier to reduce their lead time with each delivery because they feel like they are a part of your business.
Remember we discussed earlier about simplifying supply chain management?
Sometimes, using international and cross-country suppliers might cause more headaches than solutions. It might be tempting to choose them because of their discounts, but their long lead times aren’t always worth the low prices.
Local suppliers can better understand your needs and respond to them quickly. They can also offer competitive prices for great products, so you should keep them around.
It’s easy to become laser-focused on production tasks.
Point A is the starting point. Point B is the next stop. Point C is the next stop. Is it possible that one production stage can be done simultaneously?
If you can do multiple tasks simultaneously, you will save a lot of time in the long run.
Use technology to do tasks that you have to do manually. For example, tracking supplier lead times or using an estimated lead time is a disaster waiting to happen.
Automate your inventory control which will allow you to monitor inventory movement, identify trends, and understand the inventory turnover of your products.
While reducing lead times, ensure you are taking the time to do it right and not cutting corners which could lead to lower product quality.
Further Reading: Key Aspects of Inventory Control in Manufacturing Industry
To decrease lead time while maintaining a high level of product quality and customer satisfaction, you must carefully balance these two factors.
No matter how much you plan, there are always some things you can't control. For example, sometimes things just go wrong in manufacturing.
You need to account for the margin of error and stay in touch with what is happening on the ground.
Often, companies reduce the amount of time it takes to make a product, but this can sometimes mean that the product is not as good as it could be. You might be able to have two team members working on tasks at the same time, but did you know that before, they were able to help each other out with quality assurance tasks? Now they can't do that.
You might make some mistakes if you reduce lead times without thinking about all the details. This can cause problems for your customers because they won't be happy with the product quality or service. It's important to make changes slowly to keep track of what is happening and ensure that your customers are still satisfied.
You always need to think about the balance between how long it will take you to do something and how good the result will be. If you focus on one thing too much, you might not see everything else that is important. And then all your hard work will be for nothing.
What is the best way to track your progress when reducing your manufacturing lead time? This question can be answered by making small changes while monitoring your progress.
Further Reading: Quality assurance vs. quality control
An operations manager or business owner doesn't have enough time to calculate the lead time the old-fashioned way, between running the business and managing it on spreadsheets.
We suggest you use Brahmin Solutions Inventory Software and MRP Software.
How does the software exactly help?
Have a live view of your inventory levels. Brahmin Solutions has a reorder feature that allows you to set reorder points or even automate this process entirely. It can calculate reorder points based on trends and adjust weekly.
Brahmin Solutions allows you to monitor your orders in real-time, including purchases, sales, and manufacturing orders.
Order management is effortless and visual. You can see if orders are running late and make the best business decisions to reduce lead time.
Brahmin Solutions can help you figure out how long it will take to do tasks and how much it will cost to make them. Once you know that, Brahmin Solutions can help you figure out when you can deliver the products to your customers.
Brahmin Solutions production schedule updates in real-time, so if an order comes in that should take priority, you can use our drag and drop feature to rearrange the schedule. That will tell Brahmin Solutions to redistribute allocated inventory and recalculate production times.
There are many more benefits and features your business can experience by adopting a system like Brahmin Solutions.
But, we believe that seeing is believing. Come and see for yourself how Brahmin Solutions can help you lower your manufacturing lead times.
We are giving you a 14-day free trial, so you can try Brahmin Solutions in your business and see the benefits of it.
And that’s it! Everything you need to know about manufacturing lead time and the steps you can take to reduce lead time across the board.
We’re sure this article will help you, but if you have any questions about manufacturing lead time or Brahmin Solutions, please feel free to connect with us, and we’ll be more than happy to answer your questions.