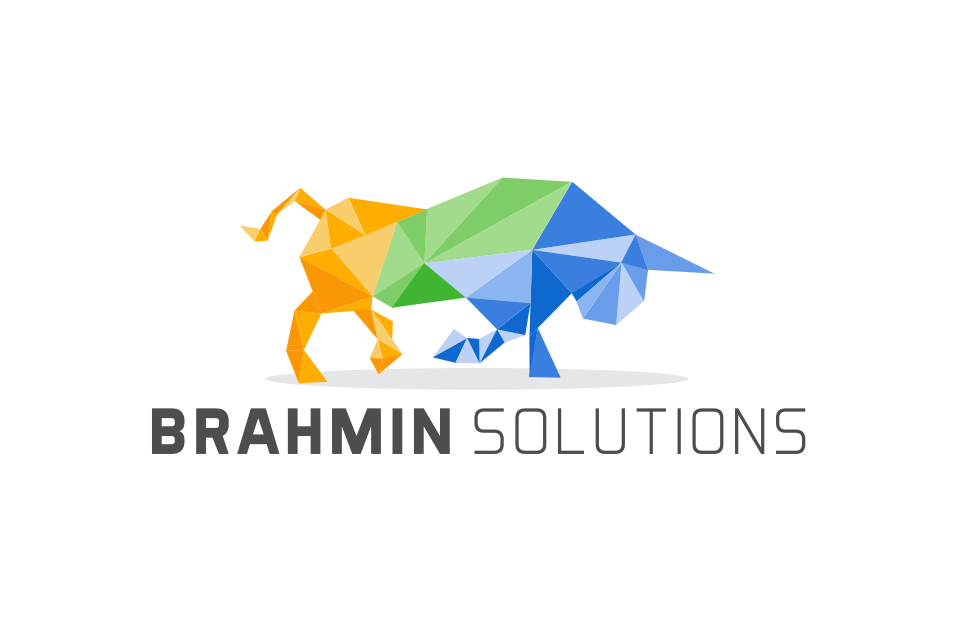
Manufacturing and Inventory Management Software
One of the most important aspects of running a manufacturing business is the ability to keep tabs on your inventory and its value. You need to know how much your stock is worth at different points in time so you can see if you will reach your revenue goals.
This article will look at the weighted average cost method to value your inventory.
The weighted average cost method is one of three ways to value your inventory stock. This method uses a weighted average to determine the cost of each available unit for sale. This method is allowed by both GAAP and IFRS.
When a business buys items for inventory, it may pay different prices. This happens because the items can be different or because they were bought at different times.
The weighted average cost method is when you divide the cost of goods available for sale by the number of units that are available. This is used when there are a lot of items that are the same, and it would be hard to say how much each one costs.
The formula for the weighted average cost method is as follows:
WAC = Cost of goods available for sale/Total number of units in inventory
Where:
Let's take a look at an example below where a company uses the weighted average method, and during the month of January, it recorded the following transactions:
The weighted average cost method results in inventory representing a value between the oldest and most recent stock units purchased.
Similarly, the COGS will reflect the cost of the oldest and newest items sold during the period.
The weighted average cost is a great way to figure out how much your stock is worth. But it might not be the best way for your business. You need to use a method that you will use all the time.
There are three other types of inventory valuation methods you should be familiar with before you choose weighted average cost (WAC) as your method of choice. These methods differ from the WAC formula, so understand how they compare before making your decision. If you change methods, it will mess everything up.
The FIFO inventory costing method is good for you if you have products that go bad quickly or products that lose value quickly. This inventory method is based on the idea that the first products bought or produced will be the first ones sold. The downside of this method is that it doesn't consider how much things cost now.
If you use the same values from past months in your accounting, and there is a significant increase in product costs, it will mean that the amount of money you make from selling products is inaccurate. This could lead to your company making less money than it should, which is bad for business.
The LIFO method records the most recently purchased products in the inventory as sold first, and the lower cost of older products will be reported as inventory. This might not always be the case because the flow of costs and physical units might not always match up.
LIFO is helpful during times of inflation. This is when the prices of goods are rising, and it's important to keep income high. LIFO also helps in times of high taxes because the costs of goods (COGS) will be higher.
The specific identification method is an excellent way to track inventory for small businesses. This is because they can afford to track every item. The method is very accurate because it tracks each item individually. However, this may not be realistic for large businesses because it can take up a lot of time and resources.
The weighted average cost method is a common inventory valuation method because it offers many benefits, such as saving time and being consistent. Here are some advantages of using WAC in your overall inventory management process.
The weighted average cost method is the simplest way to track inventory expenses. You don't need to track which batch an item belongs to or what the original cost was. You can just increase the price of all the stock units by a set amount.
The WAC method uses a blended average, which makes it easier to calculate and track the value of your stock, unlike LIFO and FIFO, which use a range of costs.
The weighted average cost method requires a single cost calculation to determine the average value of all items in stock. Since every item is valued at the same amount, there is no need to maintain detailed inventory purchasing records, which means less paperwork to keep track of.
It costs money to track inventory, whether you are calculating it manually or using software to track inventory. The WAC formula provides a time-saving alternative to calculating current inventory value, which helps you save money in the long run.
Other ways to simplify your process and reduce the costs associated with managing inventory are to use inventory management software which provides purchase order management and real-time inventory control. Optimizing your inventory management process and reordering quantity can reduce human error, spend less on labor, and save on inventory carrying costs.
If your inventory prices vary quite a bit, this might not be the best method for your purposes. If your costs have increased recently, you’ll sell less expensive items to make up for what you’re losing on the cost of more costly items. But this doesn’t always happen, and you might not recover those losses and may even end up discontinuing an item.
This method assumes that all the units are identical, but this is not always true. Some newer products may have more features or be upgraded, making them worth more than older ones. This is a problem when a supplier replaces a product with a new version and keeps the same name. The average cost method looks back over a period of time to see how much each unit costs.
It is important to be consistent when managing inventory levels. This will help make the process of filing taxes and comparing financials year over year much more effortless.
There is more to inventory management than tracking the value. The WAC method is a great way to track the value of inventory year over year. You should use this method if you are selling multiple SKUs of similar products.
Brahmin Solutions can help you avoid the headaches associated with tedious inventory management tasks. Brahmin Solutions offers inventory management and MRP software, including production management, wholesale management, order management, and data and analytics. To learn more about how Brahmin Solutions can help your business scale, check out our pricing and book a demo.