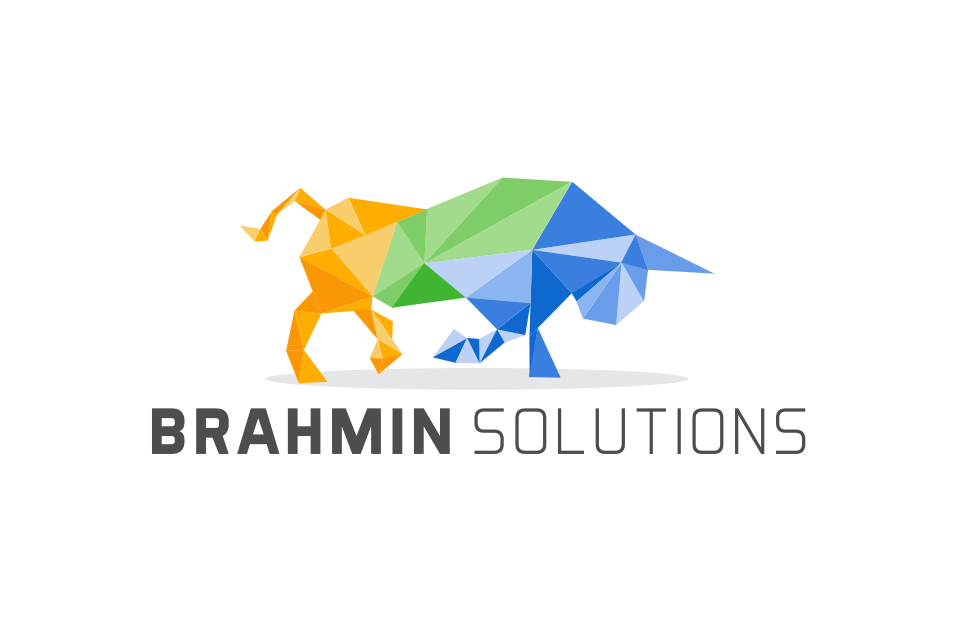
Manufacturing and Inventory Management Software
If you can't deliver products to your customers in a timely fashion, your reputation will be damaged, and you will lose money. You need to know what you have in stock at all times so you never run out of an item and disappoint a customer. Brahmin Solutions updates your inventory levels in real-time, so you always know what's available and what needs to be restocked.
It is important to keep track of all the items you have in stock. This way, you can be sure that you have enough inventory and that your products are selling well. However, the more items you have, the more complicated it becomes to track everything accurately.
That's where stock-keeping units (SKUs) come in. SKUs help you collect data about your product movements. This data can help you make better decisions about things like marketing and predicting demand for different seasons.
Brahmin Solutions part tracking software can keep you updated about changes in inventory levels. This way, you can always have the necessary parts to fulfill your customers' orders.
Stocktakes are important because they help you keep track of how much inventory you have. They can be time-consuming, but ensuring your inventory levels are accurate is worth it. You need to count the items in your warehouse every now and again to make sure you have the right amount of stock. This will help you avoid running out of products and not being able to fill orders.
Brahmin Solutions' part tracking software can help you keep track of your inventory. You can easily automate your inventory counts with barcode, QR, and RFID scanning capabilities.
You can't run your business without the right inventory. Brahmin Solutions parts inventory system can help you set minimum item thresholds for each part in your inventory.
Brahmin Solutions can take this one step further by automating reorder points by including the extra safety stock needed based on past sales and future predictions.
A bill of materials (BOM) is the data that identifies the items or raw materials used to produce any physical thing, whether that thing is a structure or a product.
A Bill of materials is a tool that helps manufacturers keep track of product development and manufacturing processes. It tracks the cost of materials used to make a product, allows manufacturers to store data for future reference, and provides a list of all the components needed to make a finished product. Bill of materials also helps manufacturers track the performance of supplier and subcontractor suppliers.
The bill of materials can also tell us which materials BOM takes the longest time to make. This might tell us there is a problem in the manufacturing process. The bill is also used for keeping track of inventory, and it gives managers information to help them make improvements.
Bill of materials software and manufacturing software is quite different. Bill of materials, or BOM, refers to a list of all the individual items and quantities needed for a project. Bill of material management is a term used in various manufacturing and MRO industries.
Manufacturing software helps you make things in a production line. It makes the process more efficient and accurate. BOM features are often included in manufacturing software as well.