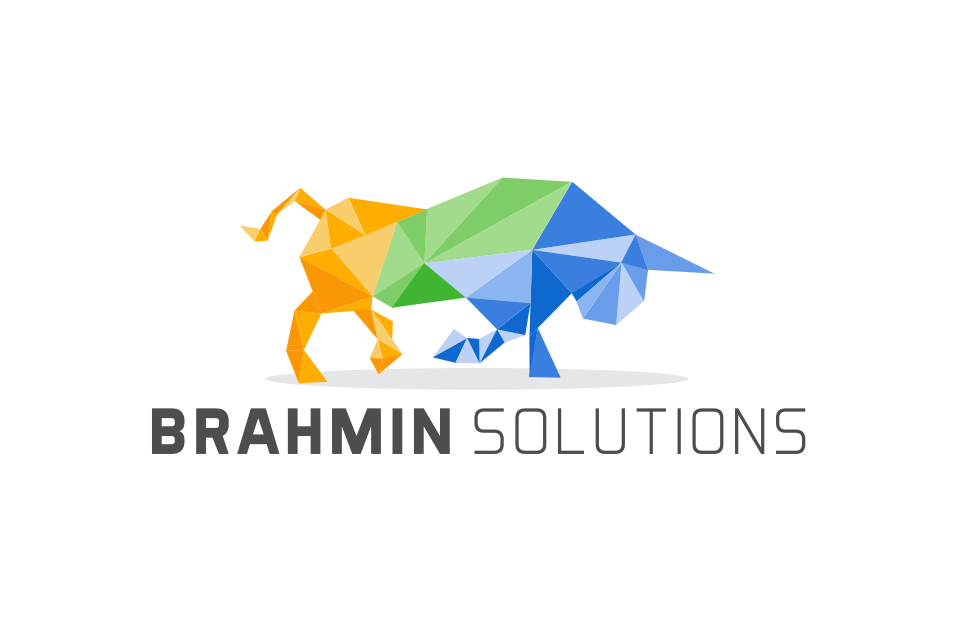
Manufacturing and Inventory Management Software
At its core, an MRP system, which stands for either Material Requirements Planning or Manufacturing Resource Planning (MRP II), is a software-powered inventory and production planning methodology. This system has been streamlining processes and enhancing efficiency in the industry for nearly three decades now. In recent times, the term 'MRP system' has also been synonymous with a manufacturing ERP (Enterprise Resource Planning) system. What sets this ERP system apart is its broader scope, introducing elements such as Customer Relationship Management (CRM) and accounting into the fray.
So, what does an MRP system do? This system is essentially designed to automate and standardize clerical tasks like data management and interdepartmental communication. It performs an essential role in collecting data from various facets of the business, integrating them into a unified system. This integration ensures that every department within the company has real-time, accurate information pertinent to their role, thus providing the so-called 'single source of truth'. For instance, inventory managers would stay updated on inventory levels and requirements, production planners would know precisely how much to manufacture and when resources would be available, and accounting could effectively manage cash flow and costs.
Knowledge is power, and in the business world, the most valuable knowledge comes from data. An MRP system ensures that all corners of your business are informed and empowered with the data they need to perform effectively.
While the above points paint a rosy picture of MRP systems, it's crucial to approach them with a balanced perspective. If you're considering implementing this software in your business, it's essential to understand both the advantages and potential drawbacks of such systems. Additionally, it's worth noting that while all MRP systems share a common goal, the pros and cons can differ significantly between different systems. In this article, we aim to provide a generalized overview of the benefits and challenges associated with MRP systems.
Like any systematic process in management, the power of a Material Requirements Planning (MRP) system lies in its disciplined application. When properly implemented, the fruits of an MRP system far surpass the outcomes of haphazard actions or reinventing the wheel, as is often the case in numerous businesses. However, it's important to understand that these benefits don't materialize overnight. Patience and consistent use are key to reaping the rewards of an MRP system.
Have you ever wondered how a Material Requirements Planning (MRP) or Enterprise Resource Planning (ERP) system could revolutionize your business communication? Let's delve in. Imagine a system that binds all your departments together, a network where everyone is on the same page. That's what an MRP/ERP system does—it serves as a business communication backbone, harmonizing all your departments into a single, unified information sphere.
Let's say a sale is in progress. The system leverages existing data to precisely predict a lead time and the overall cost of the order. Isn't it amazing how a customer order can be immediately transformed into a manufacturing order? This not only updates the production schedule but also pinpoints the ideal time for production to commence, ensuring the order is completed on time.
And what about your inventory personnel? They'll know exactly when and where materials are needed. When items are utilized in production, it's immediately mirrored in the inventory levels within the software. Now, with accurate data inputs, some systems — like perpetual inventory systems — can also perpetually update your company's balance sheets. This makes the accountants' work much easier, doesn't it?
All the data gathered and transformed into valuable statistics serves as a powerful tool for making a range of business decisions.
Ever thought about the value of standardizing your processes? This is the foundational mantra of an MRP system, and it's designed to help you achieve a harmonious rhythm in your operations. By collecting and analyzing data within the MRP system, you're not only keeping tabs on your production line but also paving the way to detect any inconsistencies or bottlenecks that might be hampering your manufacturing processes. Wondering about their root causes? The system helps you identify them, thereby enhancing your overall production efficiency.
Let's illustrate this with an example. Imagine you're monitoring your workstations’ cycle times. Suddenly, you notice a piece of equipment or perhaps an employee that isn't performing up to par with the others. Thanks to the real-time overview provided by the MRP system, you'll be able to spot these discrepancies instantly. And what's more? You're empowered to take swift corrective action, thereby minimizing disruptions and improving your supply chain management as well as your overall workflow.
Imagine being able to record every movement of your inventory and integrating your bills of materials with your inventory data. This is exactly what an MRP system allows you to do. Through this integration, the software not only pulls finished goods from stock based on your orders but also predicts raw material requirements with precision. But does it stop there? Absolutely not!
MRP systems can reduce material costs by up to 10%.
Thanks to the safety stock and reorder point functionalities coupled with low stock notifications, your business can significantly reduce shortages and avoid the cost of overstocking. Sounds good, right? But there's more.
By analyzing historical data from the system, we can identify trends and create more accurate demand forecasts. Isn't it exciting to have the ability to predict future needs based on past trends? Plus, with the backward scheduling functionality, you can implement the just-in-time model. This fantastic feature allows you to order raw materials at the last possible minute, ensuring they arrive precisely when needed in production. This not only minimizes waste but also maximizes efficiency.
Have you ever considered the power of software-assisted inventory and production tracking? It significantly enhances traceability within your supply chain. Imagine a system where every event creates a digital footprint. This traceability allows you to pinpoint inconsistencies right back to their origin, streamline product recall processes, and effectively eradicate the causes of product non-conformity. This level of control is not just beneficial but essential in highly regulated industries like food, pharmaceuticals, and automotive sectors.
Imagine having a wealth of real-time data at your fingertips. This is precisely the power that an MRP system provides, enabling you to fine-tune your cost structures, inventory levels, and staffing strategies. The result? A flexible, efficient business that stays ahead of the curve. MRP systems are ideal companions for a variety of inventory control techniques, offering a wealth of data that enhances the accuracy of calculations such as MOQ, EOQ, safety stock, and ABC analysis. The integrated production scheduling software in MRP systems provides critical insights into material and staff requirements, helping you identify if you're underutilizing or overextending your production capacity. Some MRP solutions even offer an integrated accounting module, providing a clear view of your company's financial health and potential cash drains. Who wouldn't want such a tool in their arsenal?
With an MRP system, you can automate a multitude of clerical tasks, freeing your workforce to focus on more strategic initiatives. Imagine replacing the tedious pen-and-paper inventory management methods with efficient barcode scanners integrated with your MRP software. Capacity planning and production scheduling are handled automatically, providing your production managers with more time for enhancing efficiency. Automated data entry and calculations minimize the risk of human error, while automated information sharing reduces miscommunication between departments, suppliers, and customers. For manufacturers of complex products, the multi-level BOM functionality allows calculating material requirements and creating manufacturing orders for hundreds of sub-assemblies in just a few clicks. Isn’t that a game-changer?
What do customers value the most? Delivering their orders as promised - right on schedule, in the correct quantity, and at the agreed price. This might seem like a tall order when dealing with multiple data sources and relying on intuition for lead times and costs. However, with an MRP system, these calculations become automated based on your current inventory levels, supplier lead times, and available production capacity. This results in accurate deliveries becoming the norm, not the exception. Even if unexpected roadblocks arise during production, you can promptly notify your customers about potential late deliveries, enabling them to adjust their business plans accordingly. By facilitating effective communication, you can boost customer satisfaction, potentially leading to increased business and a more significant bottom line. Isn't that the kind of relationship you want with your customers?
In contrast to traditional pen-and-paper methods or cumbersome spreadsheets, MRP systems provide an unparalleled avenue for scalability. Such systems can be effortlessly scaled in tandem with your business, thus offering the much-needed flexibility in the dynamic and fast-paced business landscape of today. Can you imagine managing hundreds of bills of materials (BOMs), thousands of SKUs, and a plethora of suppliers and customers, not to mention your own team members? It's quite the Herculean task, isn't it? Fortunately, the use of a robust manufacturing resource planning software simplifies this daunting task by leaps and bounds, enabling you to scale your business as and when required.
While an MRP system is a powerful tool with significant benefits, it's only fair to acknowledge that it does come with some potential drawbacks. However, these can be effectively managed with careful planning and meticulous execution of the implementation process.
Deploying an MRP system goes beyond merely covering the cost of the license or subscription. It's a process that requires an investment of time and resources. The time spent on assessing different solutions and the reallocation of staff from their usual duties to focus on implementation are factors to consider. If you choose to hire an implementation consultant, remember that their fees could, at times, surpass the actual cost of the software. Sound daunting? It doesn't have to be, with the right planning and resource allocation.
Before you even start to browse through software options, it's critical to map out your business needs in detail. If you don't, you run the risk of selecting an MRP system that's not the right fit for your company. This mismatch could either prevent you from realizing the full potential benefits or turn the software into a financial drain due to complex implementation and usage. Your ideal MRP system should offer all the functionalities you need, at a price that fits comfortably within your budget, and with a user-friendliness level that matches the IT skills of your team.
Introducing software that impacts the entire organization isn't a task to be taken lightly. It demands the buy-in of not just department heads, but also the broader team. Business processes often need to adapt to the new software, rather than the other way around. This can sometimes ruffle feathers among employees who are comfortable with their current workflow and hesitant to change what they perceive as "not broken." However, with compelling arguments and clear communication, it's possible to rally everyone around the benefits the software will bring to both the individuals and the organization.
Have you ever been cautioned about the potential data accuracy risks associated with an MRP system? You might've heard that consistent and accurate data input is crucial. Any inconsistencies or inaccuracies might lead to lackluster or even damaging results. However, is this risk exclusive to MRP/ERP systems? Let's consider that.
Even when managing your business the old-fashioned way, with a pen and paper, errors can and do occur, perhaps even more frequently. In truth, an MRP system actually simplifies the process of detecting and correcting data entry errors. It provides a streamlined navigation through the data labyrinth, making it easier to locate and rectify any inaccuracies. And the beauty of it? As soon as you fix an error, the correction is automatically reflected across all areas impacted by it. This makes the process of rectifying mistakes quicker, less arduous, and ultimately, less costly for your business.
Implementing Data Validation Measures: One effective way to ensure data accuracy is by implementing data validation measures. Data validation is a process that checks the accuracy and quality of data before it's processed. This can include measures such as range checks, format checks, and consistency checks, among others. It might seem like a daunting task, but remember, the benefits of accurate data far outweigh the costs of inaccurate information.
There are numerous software providers in the market catering to manufacturers, with new ones consistently emerging. This can be beneficial if you have clear software criteria, but it becomes more challenging to find the perfect solution if your requirements are vague. Prior to searching for an MRP system, a company must consider these factors:
Choosing the right MRP system can be a daunting task. But remember, the goal is not just to find a tool that does its job but to find a companion that supports and enhances your business operations. Could Brahmin Solutions be this companion? Book a demo to learn more.