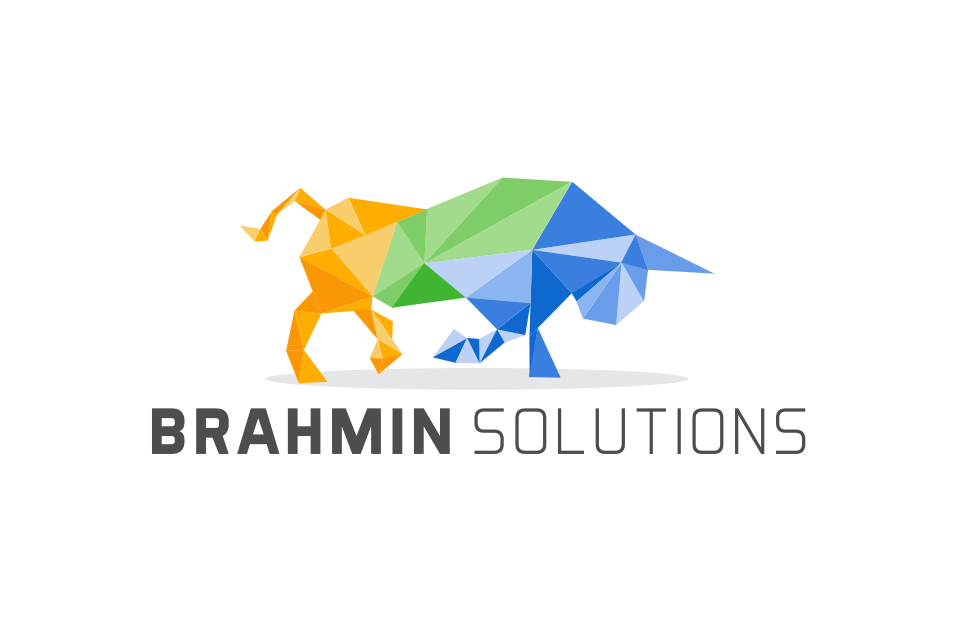
Manufacturing and Inventory Management Software
As a manufacturer, if you are targeting a lean manufacturing process, you need to get rid of inventory waste. It is one of the critical elements that act as a barrier to your manufacturing processes of becoming leaner and more ROI driven.
The manufacturing industry loses a lot of money every year due to the overstocking of inventory. At the other end of the spectrum, losses also occur due to understocking and even the unavailability of raw materials (again an outcome of poor inventory control of the raw materials).
And, it is important to think of inventory management as a technique that helps you save money by decreasing overheads. It needs to be an essential element of your business growth strategy. If you go about it in the right manner, it will improve your cash flow, which can then be invested in other revenue generation activities.
Maximizing the potential of your inventory results in improved business profitability – You make better business decisions, which results in improved business outcomes.
There are plenty of challenges that the manufacturing industry encounters when it comes to inventory control. However, if you are to pick some of the key challenges, then the focus must be on stock valuation, stock management, and control.
One needs to understand that manufacturing facilities are massive in scope and scale and typically have large warehouses that are a part of these facilities. The problem stems from the fact that stocks are managed by humans with very little technological intervention.
What’s more, the availability of stock and its replenishment is typically dependent on judgment calls made by humans rather than advanced tech-enabled stocktaking and the application of scientific models.
This results in a human error as it becomes substantially difficult to calculate key stock aspects such as stock levels, lead time provision, and oversight in the internal control systems that govern the various aspects of stock management.
Another problem that results from a human-based approach to managing inventory is the tendency to overestimate or underestimate stock availability, especially in the case of raw materials. In such cases, purchase orders are placed more than their demand, which can result in the manufacturer incurring holding expenses, which over some time, can result in tremendous losses.
We are also looking at manufacturing moving from assembly line production to more made-to-order production wherein, and all products are tailor-made according to end-customer specification. As can be imagined, in this particular case, stock forecasting goes for a toss, as one cannot predict the demand for such products. But does this mean inventory cannot be managed optimally?
No, it doesn’t.
The focus should be on deploying manufacturing industry-specific inventory control software that has been configured to address inventory control challenges in manufacturing.
A manufacturing plant is relatively complex, and this complexity is based on the domain, whether it is churning out retail goods, food, heavy machinery, automobiles, or something else. If you are a manufacturer or even thinking about getting into manufacturing in a big way, you need to understand the critical aspects of inventory control that will make you make better inventory control decisions.
Let’s get started, but before that, here’s a question that must be answered:
It is essential to understand that inventory in the manufacturing industry is markedly different from that of inventory, in say, an eCommerce organization or even retail.
Manufacturing inventory includes raw materials, which are items that are used to make the finished products. In the case of raw material inventory, these are items that are not yet a part of the production process.
Then there are the raw materials that are being used in the production process or might be used in the production process, next after the current production batch is complete. These are known as WIP or Work-In-Progress.
This is followed by an inventory that is composed of finished products that result from the production process, and which are ‘ready to be sold’ items. These items can be housed at the manufacturing facility and a central warehouse or different warehouses (we are talking about inventory in distributed locations here).
You also have an inventory (finished products) that is ready for distribution, which means it is made up of items that immediately become a part of the larger supply chain.
And finally, manufacturing inventory also includes maintenance goods and operational supplies; these are items that are used to maintain the production process and ensure its seamlessness. These include tools, cleaning supplies, and more.
As can be imagined, managing this complex and diverse inventory is going to be extremely challenging.
In the face of this complexity, how can manufacturers gain control over their inventory? What are the considerations they must keep in mind to ensure their inventory management doesn’t go for a toss?
Let’s take a look:
The starting point of any inventory control overhaul is to minimize human intervention throughout the inventory management process. The focus should be on shifting to an automated process that is enabled by the deployment of inventory control software, specifically catering to the needs of the manufacturing industry.
The critical components of this shift include not only bleeding-edge inventory control solutions but also equipment such as RFID, IIOT, and barcode scanners. The idea is to use technology to make inventory management far superior than it was before.
When it comes to the raw materials you are using for production and the final products, it will be a massive benefit if you put a system in place that offers you real-time tracking of your inventory items right through the production process.
From the time they reach your manufacturing facility, till the time the final product is delivered to the customer, you need to be able to keep track of every item of your inventory.
This tracking helps you trace your inventory right from delivery to its use. This allows you to enhance your order processing and also product recalls. The use of a cutting-edge inventory management software in this particular case digitizes information. It ensures end-to-end inventory detail that updates you about inventory status all the time.
What you are aiming for is getting through visibility into the state of your raw materials, raw materials being used for production (Work-In-Progress), and finished products.
One of the ways manufacturers achieve such control is through serialized barcoding. The benefit of such serialization is that they had complete knowledge of the quantity of raw material when it was sent in for production, how much was used, and more.
This unprecedented insight into your inventory can help you make better business decisions as you now have accurate real-time inventory status. This enables you to reduce your inventory-related expenses.
There are times when, even in a best-case scenario, the inventory management plan can change. There might be a disruption at the raw materials’ supplier’s end, or there might be an issue with the product line, or the market demand for a product might have increased or decreased.
Such scenarios will disrupt the existing workflow pattern, and it is of critical importance that this change in workflow is taken into consideration in the inventory control process.
The idea is to ensure that all key stakeholders in the inventory control and management process are immediately notified by way of emails, texts, or push notifications when unplanned changes can impact the inventory.
Take for example, a case wherein your raw material supplier has sent an incorrect order – the order shipped is significantly lesser than the demand.
What happens?
If there is very little awareness amongst stakeholders, the production line will continue to churn out the same number of products as before. Still, very soon, the scarcity of raw materials comes into play. This impacts the production schedule and all other upstream decision makings, including sales and marketing.
Here’s another example of why disruption alert is so crucial.
If you do not keep detailed inventory data and haven’t put a mechanism in place that alerts you in case of inventory changes, you might not realize that a part of your inventory has expired. What if you realize this just a few days before an order is due to be shipped?
Chaos!
However, if the disruption was identified and conveyed to the right people at the right time, a decision can be quickly made to source raw materials from a different supplier, thus ensuring unimpeded production.
Meeting the highest standards of inventory control and management is not an end goal in itself. The goal is to ensure optimal inventory to facilitate optimal production. Inventory control plays a huge role in planning the production process from the ground-up.
With proper inventory management controls in place, you have the necessary information to plan your production; this information can include inventory data, the cost of raw materials (not just sourcing, but also warehousing costs), availability of raw materials, and much more. This data helps plan the production process in a more streamlined manner.
Forecasting and Planning
This is yet another highly critical element of inventory management in the manufacturing domain. As a manufacturer, you will need to plan your production budget before the start of every financial year or at times before the beginning of the quarter.
For this to happen, you will need to forecast the demand for your product, which then helps you maintain an adequate supply of raw materials.
It is product demand that helps you calculate optimum levels of inventory. But in order to maintain ideal inventory levels, you need a purchase a system in place that automates the process of placing purchase orders.
This is done keeping the ‘demand forecast’ in mind at all times. Contemporary inventory control systems don’t just stop at automating inventory purchases but also keep various other requirements in mind. E.g., there might be a case wherein a vendor demands a minimum order be placed; a purchasing system will keep this in mind.
Smooth and Precise Scheduling – No Scheduling Conflicts or Errors
Your manufacturing unit might have multiple clients, wherein the product demand varies from one client to another. What’s more, in the course of a year, the demand fluctuates, considering changing the buying behavior of consumers, economic pressures, and various other factors.
Also, each client will have different demands when it comes to scheduling product deliveries.
You will be unable to keep on top of this scenario in the absence of proper inventory control. Your staff will be hard-pressed to manage order details coming from different vendors. Again, managing and maintaining optimum inventory levels (in this case – finished products) will help you cater to even the most demanding clients.
Sorting out Warehouse Challenges
Big manufacturers or even small manufacturers, who are looking to scale their operations, face warehousing challenges. One key challenge is managing warehouse space in the most optimum manner possible.
Many manufacturers also have to contend with lost warehouse inventory. Some also have to suffer the consequences of damaged inventory. These and many other challenges have one common solution – Better warehouse management through optimum inventory control.
It is imperative that you are able to manage your warehouse stock, meaning you must have in-depth clarity on the kind of stock that exists in your warehouse – the nature of the stock and its amount.
There are occasions when manufacturers find that their warehouse doesn’t have enough space for finished products, because they overstocked their raw materials, or they might just find they ordered raw materials that they didn’t need. Reason – they couldn’t find the raw materials they wanted, because these were stored in the corner of the warehouse.
These are situations they won’t find themselves in if there are proper inventory and warehouse management systems in place.
We have discussed the importance of inventory control in the manufacturing industry and the various challenges that can be solved through the use of proper inventory control methodology. There is a reason why we thought of discussing this important aspect of the manufacturing process. It can play a huge role in determining the ROI and profitability of your manufacturing unit.
If you are looking to improve the inventory scenario in your manufacturing facility, it is first essential to identify the challenges you are facing and the outcomes you expect. Then go about searching for the inventory control system that you feel best fits your needs and requirements.
Understand this system, its features, and only then deploy it to control and manage your inventory.