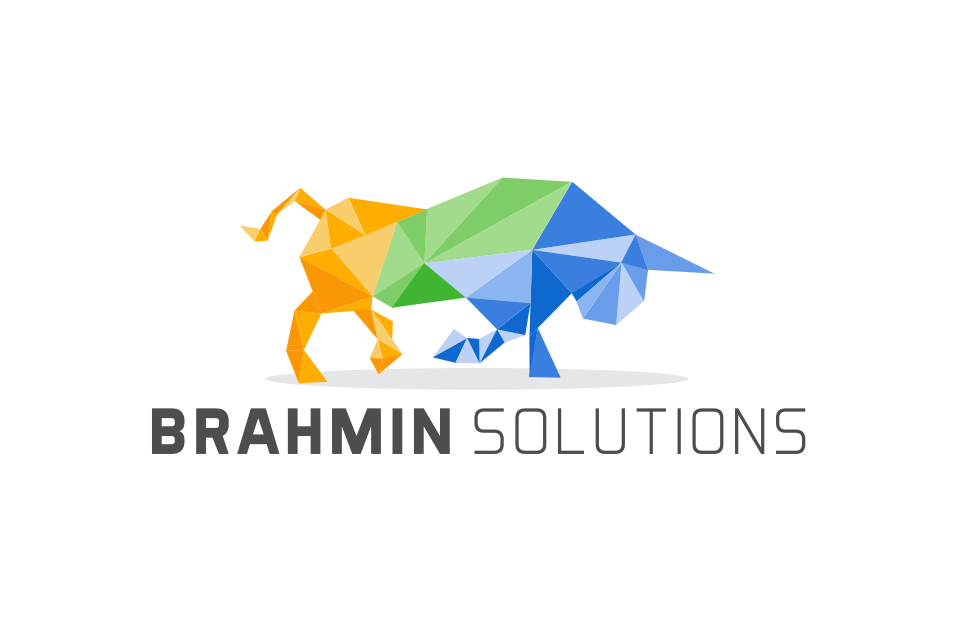
Manufacturing and Inventory Management Software
A master production schedule sits at the core of every successful manufacturing business. It’s a critical piece of the puzzle, keeping every level of your operation aligned.
So... what is it?
If you keep hearing the term “master production schedule” thrown around and aren’t sure what it means, this guide is here to help. We’re going to cover what a master production schedule is, how you can make one, what its benefits are, and more.
A master production schedule is a document that keeps track of everything you’re manufacturing. In it, you’ll find product quantities, schedules, and specifications. At any given moment, you should be able to check your MPS and know what you’re manufacturing, how much of it, and when.
As you can see, this is why master production schedules are touted as being so essential to the way manufacturers operate. It’s your central point of truth, keeping everyone on the same page and everything organized.
And, more importantly, when things aren’t organized, it’s a place you can return to and better understand where things are going wrong.
Beyond its core functions (keeping track of your entire manufacturing process and needs), a master production schedule provides a few primary features.
First, a master production schedule saves your resources. It does this by reducing the amount of time you need to manage your production flow. At any given time, this is a process that can take hours.
The less time you spend managing your production flow, the more money you’re able to save. Additionally, reducing the time spent managing your production flow minimizes the potential for errors and slowdowns.
Anyone involved in the management side of manufacturing knows how complicated a balancing act it is. You have to keep track of dependencies, supply and demand, capabilities, resources, budgets, shipping and manufacturing timeframes, materials, labor, and more.
Managing all of these factors is more than overwhelming — it’s critical. That’s why one of the basic functions of a master production schedule is to address this need.
An MPS helps unify and organize these demands in a single location. You can keep track of every facet of your manufacturing process and timeline, ensuring that nothing is running over or into anything else. And it’s shareable, so you can be sure that all other stakeholders can view these details as well.
Adjusting your manufacturing schedule is never easy. It involves shuffling around all of the factors mentioned above, if not more. And it needs to be done in unison to avoid unpredicted outcomes.
Without a master production schedule, it can be challenging to account for and anticipate everything that a schedule adjustment can affect. With an MPS, it’s just a matter of carefully reading through the schedule and accounting for each item.
Finally, a master production schedule is incredibly helpful in preventing stockouts. A stockout is something that everyone involved in your manufacturing chain (including the customer) wants to avoid. It slows down your entire operation and hurts your sales.
Using an MPS, you can make more accurate predictions on your production capabilities and future demands and create more robust plans for when an unexpected stockout occurs.
A master production schedule is not necessarily a single schedule but a combination of a few different plans and schedules. Below are the three core plans that should make up your MPS.
The first part of a master production schedule is the demand plan. A demand plan accounts for all the demands on your manufacturing chain and the factors that go into those demands.
Demand is what drives the supply chain, and so it’s crucial to account for and plan for its impact on your manufacturing processes. That includes tailoring your capacity to lulls in demand as well as ticking your demand plan up with the market without overextending your capabilities.
Rough-cut capacity planning involves predicting your long-term manufacturing capabilities. You will look at the suppliers and manufacturers currently involved in your operation and come up with a rough estimate of your maximum capacity with these resources.
In a master production schedule, your rough-cut capacity plan prevents you from exceeding your manufacturing capabilities. It’s a common mistake to order more materials or products than you can produce. A rough-cut capacity plan keeps this in check.
The third component of a master production schedule is the production plan. Production planning is where you directly allocate resources, materials, and labor to manufacturing products. Rather than a predictive or preventative plan, you can think of this as your “active” manufacturing plan.
As a result, your production plan’s success is mainly dependent on the quality of the rest of your MPS.
The first step in creating a master production schedule is to make your demand plan. To build a demand plan, you’ll need to account for current demand and forecast future demand. This will involve a lot of research and should be done collaboratively.
Remember that you will note your manufacturing capacity in a different piece of your MPS, so don’t worry about that yet. It’s alright if your demand plan exceeds your capacity. This plan is only meant to later inform your active production plan.
Next, you should identify all the raw materials required throughout your manufacturing process. If your manufacturing chain is already up and running, this should be a bit easier; just note down the raw materials you’re already sourcing.
If you’re preemptively building an MPS, however, you’ll want to identify and source these raw materials simultaneously. This will help you create the list of materials, ensure that you can source them, and help with assessing your capacity later on.
After that, you should be ready to create a rough-cut capacity plan and a production plan. This is just an initial draft, so don’t worry about making mistakes; you’ll be checking for these and rooting them out in the next step.
The goal in drafting the remainder of your MPS is to strike a balance between your capacity limitations (covered when you identified the raw materials you’ll need and with your rough-cut capacity plan) with the demands forecast in your demand plan.
The next step is to check your draft production plan against your demand plan and rough-cut capacity plan. Do you have the capacity to fulfill this plan? Or is there extra headroom?
After that, the logical step is to align your production plan with your resources and demand plan. That means cutting your production plan back a bit or scaling it up, depending on the relationship between your expected demand and capacity. If you’re inexperienced with creating a master production schedule, then leaving yourself a bit of room for error is recommended.
The last thing you want is to go through all of this trouble only to have the various teams fall out of sync. Make sure everyone involved has a copy of your master production schedule, understands it, and provides input on it if they have any.
Finally, you’re ready to put your master production schedule into action. Now the only thing left to do is keep your eye on it. Consistently check in with your performance, output, changing demands and capacities, and see whether or not your MPS is keeping up. If it isn’t, continue to make adjustments until it’s functioning as expected.
Now that you know what a master production schedule is and how to create one, you’re ready to reap the benefits that an MPS has to offer. Here are just a few of the immense benefits you can expect moving forward.
Having a master production schedule in place means you’ll have a much more accurate idea of what you need to produce. You’ll be able to anticipate and match demands and shortages with more confidence and success.
Agility is critical in today’s market, and that’s something that an MPS can provide. Whether you’re using a Make-to-Stock, Make-to-Order, or Assemble-to-Order workflow (or even switching between them), an MPS will make moving from one to the next far simpler.
Finally, a master production schedule will help you schedule your product batches with improved accuracy. You’ll be able to plan farther in advance with fewer errors, losses, and stockouts.
Managing and creating a master production schedule is easier said than done. To be successful in this endeavor, you’ll want to use the latest methods and tools available.
Reach out to the team at Brahmin Solutions today and see how our tools can help you succeed.