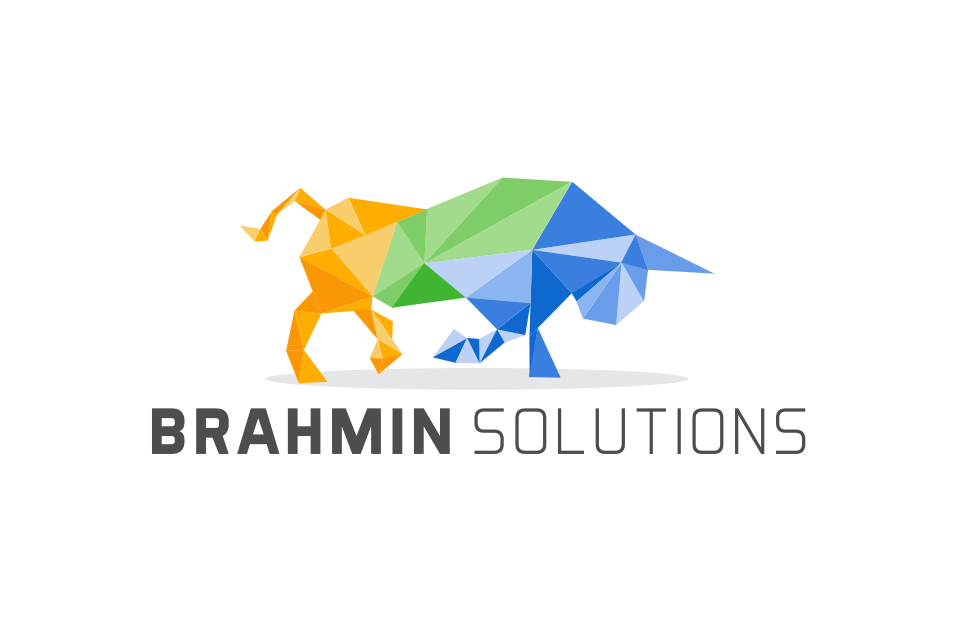
Manufacturing and Inventory Management Software
Imagine you're the conductor of a symphony, but instead of managing musicians, you're orchestrating the flow of materials in a manufacturing setting. Welcome to materials management! This strategy is all about the harmonious planning, coordination, and control of everything from procurement to storage, handling, and use of materials.
The endgame? To ensure the right materials are at the right place, in the right quantity, at the right time, and in the perfect condition, all while keeping costs low and efficiency high. The materials manager is the maestro, pulling together inventory, purchasing, and production and setting up the communication lines to keep material requirements and supplies flowing smoothly down the supply chain.
Now, depending on the organization, materials management might play a different tune. Some companies see it as a subset of procurement management, while others view it as its own entity serving different business areas. Still, others might split the responsibilities of materials management between departments like procurement, supply chain, logistics, and so on, often seen in larger manufacturing or construction enterprises.
As part of procurement management, materials management is your one-stop shop for all things related to sourcing and purchasing. But, if it's seen as a separate part of supply chain management, it bridges the gap between procurement and production. Here, it's more about material requirements planning, coordinating material deployment and replenishment, and ensuring quality control and inventory analysis for direct materials.
Speaking of materials, there are two types in the manufacturing world: direct and indirect. Direct materials are the ones that go directly into the products a company makes, like rubber in tires or fragrance in soap. Indirect materials, on the other hand, are used in the manufacturing process but don't make up the product itself, like adhesives, staples, equipment, or spare parts. In any case, materials management takes care of controlling the flow of both types.
Take the stress out of managing your materials with Brahmin Solutions.
So, you've heard the term "Sustainable Materials Management" (SMM) thrown around, and you're a bit curious. Good news! You're in the right place. Let's unpack this seemingly complex term.
At its core, SMM is all about using and reusing resources as productively and sustainably as possible over their entire lifecycles. It's like a well-choreographed dance between materials and the environment. The aim? To minimize environmental impacts and conserve resources.
SMM isn't just a fancy term, it's an approach that helps businesses manage their materials from design and manufacture to use, re-use, and recycling. It's all about thinking ahead, designing products that can be reused, and making the most of resources. SMM is like the ultimate recycling system, but on a grand scale.
Materials management, as per the U.S. Environmental Protection Agency (EPA), is a concept that beautifully intertwines our economic prosperity and environmental wellness. It's all about:
Materials management isn't just a strategy, it's a mindset shift. It's moving away from the old 'take-make-waste' model and towards a circular one where materials are given new life through reuse, recycling, or composting. The grand vision of materials management? To ensure that our use of materials aids in building a sustainable future for our planet, boosting not just environmental health, but also economic growth and social wellbeing.
Think about a soda can. With SMM, the goal would be to design the can so that once you're done enjoying your beverage, it can be reused or recycled with as little environmental impact as possible. It's about making the most of what we have, and leaving as little footprint as possible.
There you have it! A nutshell explanation of Sustainable Materials Management. It's a fascinating concept that's reshaping how businesses think about their materials and resources. And who knows? It could even help your small business become more sustainable and efficient. So why not give it a whirl?
Think of your business as a well-oiled machine. Each part has a specific function, but the machine can't work effectively if one part is missing or underperforming. In the context of materials management, inventory management is that critical cog in the machinery that helps keep operations running smoothly.
Imagine running a bakery and suddenly finding out you're out of flour in the middle of a busy day. Not a pleasant scenario, right? Inventory management prevents such situations. It involves diligently tracking what's in stock, what's running low, and what needs to be reordered. This way, you're always prepared and never caught off guard.
Did you know that holding excessive inventory can lead to high storage costs and potential wastage? Inventory management comes into play here by ensuring you maintain an optimal balance. It helps you avoid stocking too much or too little, thereby reducing costs and minimizing wastage.
How many times have you walked away from a business because the product you wanted was out of stock? Inventory management helps avoid such customer dissatisfaction. By ensuring a steady supply of products, you can meet customer demand promptly, enhancing their overall experience and loyalty.
What sells more? What doesn't? When is the demand highest? These are just a few of the questions that inventory management can answer. By providing insights into sales patterns and customer behavior, it can guide strategic decisions such as what to stock, when to reorder, and how to price products.
Remember, effective inventory management is the backbone of successful materials management. It ensures you have the right materials at the right time and in the right quantities, thereby supporting seamless operations, cost efficiency, and customer satisfaction.
Imagine the ripple effect that effective materials management processes could have on your business. Intriguing, isn't it? Well, that's just one of the many benefits you can anticipate when you dive into the world of materials management.
Effective materials management involves obtaining the appropriate amount of materials to optimize purchasing procedures and reduce unnecessary expenses. By purchasing the right materials in the right quantities, companies can avoid waste and achieve substantial cost savings. Effective materials management can lead to a 20% reduction in procurement costs.
Imagine materials management as a balancing act. It’s all about keeping your inventory levels just right – not too much, not too little. This way, you dodge the pitfalls of overstocking and shortages, sidestepping unnecessary storage costs or panic buying. The result? A smooth-running, cost-effective operation.
Imagine an organized, smooth-running warehouse where every inch of space is put to good use and costs are kept at bay. This isn't just a dream scenario - it's the reality with effective materials management. It's your secret weapon to unlock remarkable operational efficiency.
Picture this: Your business is a high-powered vehicle, cruising into the future with a finely tuned engine, where each component fits flawlessly, and the motor purrs with peak efficiency. This is the magic of skillful materials management. It's akin to having a crystal ball, offering you a sneak peek into the future and allowing you to predict the demand and supply of materials accurately. No bumps, no hitches - just smooth operations and clear skies ahead.
That's what effective materials management can do for you. It's like a crystal ball, letting you peek into the future to forecast the demand and availability of materials accurately. No hiccups, no interruptions - just smooth sailing.
But wait, there's more! Not only does this precision planning reduce downtime, but it also turbo-charges your operational efficiency. Think of it as the secret sauce that ensures your production processes run like clockwork. And the cherry on top? Your customers will be grinning from ear to ear as on-time deliveries become your new normal, not a pleasant surprise. Now, that's what we call a win-win!
Implementing materials management in your small business can lead to substantial cost savings. Efficiently managed materials lead to fewer wasted resources and lower procurement costs. This translates to more pennies in your pocket – and who doesn't love that?
Companies with effective materials management practices have a 15% reduction in inventory costs.
With materials management, the quality of your products can significantly improve. By having a clear understanding of your materials and their lifecycle, you're better equipped to monitor their quality and performance. A higher quality product? Yep, that's a big win for your customers and your reputation.
Unpredictability in business can lead to sleepless nights. Thankfully, materials management can help lower those stress levels. With a clear, well-organized system, you can better predict your material needs, quantities, and costs, reducing unforeseen complications. Less unpredictability equals more peace of mind!
Materials management isn't just about immediate benefits. It's also about looking to the future. By optimizing your use of materials, you contribute to more sustainable practices, reducing waste and environmental impact. A win for your business today, a win for the planet tomorrow.
And there you have it. Materials management isn't just a fancy term; it's a critical business practice with tangible benefits. So, why wait? Start implementing materials management in your small business today, and reap the rewards tomorrow!
To improve operational efficiency and sustainability, there are a number of best practices that can be implemented for effective materials management. Here are a few important ones to consider:
Imagine being the captain of a ship, navigating the vast ocean of quality control and raw material purchasing. That's the role of a materials manager! But even the most skilled captain can't steer the ship alone. They need a reliable crew that follows standard operating procedures to the letter.
These procedures are the map to treasure - they detail material specifications, quality standards, and sourcing requirements. By adhering to these, the crew can maximize product conformity (the treasure!) and minimize non-conformity (the pesky pirates!).
Quality control should start before production and be performed regularly. Quality failures can be costly, especially when detected by the customer. It's important to partner with reliable suppliers capable of providing appropriate materials in the correct quantities and on time. Suppliers should be evaluated on cost, quality, reliability, and sustainability practices. Good quality enforcement can be more affordable than rectifying quality failures.
For efficient factory operations, knowledge of material location and quantity is crucial. Proper markings and organized storage are important in managing physical stocks. Regular physical counts help identify issues, while technologies like inventory or MRP software assist in daily inventory tracking.
For an average manufacturer, a significant chunk of their expenditures stems from direct material costs. With this in mind, it's imperative to ensure that surplus inventory isn't sequestering funds that could be better utilized elsewhere.
Remember, having inventory tied up for too long can lead to the unfortunate circumstance of goods perishing or getting damaged. This is especially relevant for materials with a definitive expiration date.
Manufacturers should give thoughtful consideration to various inventory valuation methods - for instance, FIFO (First In, First Out), LIFO (Last In, First Out), or Weighted Average. The chosen method should align seamlessly with the specific nature of their business operations.
Material planning is crucial in materials management. It begins with demand planning, which forecasts the product quantities to be sold in a certain timeframe. Using your product's bills of materials, you can evaluate the material requirements for this period. By assessing what materials are already in stock, you can determine what additional materials need to be ordered. This information helps create a delivery schedule to ensure a steady supply of raw materials and prevent work stoppages due to material shortages.
By utilizing established inventory control techniques, you can gain valuable insight into the performance of your SKUs. This knowledge can assist you in reducing your inventory costs.
Ever heard of the 80/20 rule, also known as the Pareto principle? It's a game changer in inventory management. By leveraging this principle, ABC analysis helps you to classify your SKUs based on their consumption value. It's like sorting out your wardrobe, but for your inventory!
Category A is like your favorite jeans. These are the top 20% of SKUs that contribute to a whopping 80% of your total consumption value. They are your star performers and deserve the most attention – think higher service levels and frequent reviews.
Next, come your B-category items. These are your reliable t-shirts, making up about 30% of your SKUs and contributing to around 15% of the total consumption value. They may not be as glamorous as your A-category items, but they still need more attention than your C-category items.
And then we have category C – these are the items that only makeup 5% of your total consumption value, even though they account for about half of your SKUs. They're like the old socks in your wardrobe, not getting much attention, with the least amount of resources allocated.
But what if sorting your items into these three categories feels too simplistic? That's where XYZ analysis comes in. It allows you to account for the varying consumption patterns of your SKUs, adding another layer of insight to your inventory management.
Think of safety stock as your safety net - a stash of materials you keep on hand to dodge inventory shortages and keep production humming along. It's your plan B when the unpredictable happens in the supply chain due to changes in supply or demand.
The reorder point is like your alarm clock. It's the predetermined inventory level that triggers an order for a particular SKU, signaling it's time to top up your stock.
Now, setting just a reorder point could land you in a pickle. If delivery times overshoot the expected time to a stock-out, your materials will run dry, and production will hit a pause until new materials roll in. That's where your safety stock steps in to save the day. But remember, these aren't arbitrary numbers. They need to be calculated with precision to ensure they're providing maximum value to your business.
Imagine if you could streamline your manufacturing process so that your product barely has a chance to gather dust before it's whisked off to the end consumer. This is the magic of Just in Time (JIT) - not just an inventory control method, but an overall approach to manufacturing. It's all about minimizing the time your product spends in the supply chain, helping manufacturers dodge the pitfalls of overproduction, bottlenecks, and surplus inventory.
When we bring JIT into the world of materials management, it's like a breath of fresh air. The principle is simple - provide materials exactly when they're needed, matching demand as closely as possible. The result? A seamless flow of materials, drastically reduced inventory levels, and a significant cut in holding space and costs. It's efficiency at its finest.
Imagine having all the ingredients of your favorite recipe pre-measured, bundled, and ready to go. That's what material kitting is all about! It's the art of neatly packing all the elements of a Bill of Materials (BOM) into an easy-to-use kit, even before it hits the production floor. This savvy technique not only simplifies your line-side inventory but also turbocharges your picking speed, reporting, and quality control processes.
So, when does kitting shine brightest? Well, it's like a secret weapon when you're juggling a large medley of tiny components, crafting customized products with a multitude of variables, or when you're playing Tetris with limited space on your shop floor that can't accommodate much line-side inventory.
Further Reading: The complete guide to product kitting
Imagine a world where manufacturers and materials managers have a wealth of technological tools at their disposal. These include Barcoding, RFID and IoT devices, and warehouse management software, all designed to keep a tight rein on inventory. But the real game-changer, the tool that brings everything together not just in materials management but across all departments of a manufacturing company, is a manufacturing ERP system.
What's the magic of a top-notch manufacturing ERP? Well, it allows manufacturers to unite their entire business within one single application. This covers aspects of material management like material requirements planning, material deployment and replenishment, supplier management, quality control, inventory control and analysis, kitting, and so much more.
But that's not all. A manufacturing ERP system also simplifies other key manufacturing operations management processes. Think production planning and scheduling, order management, return merchandise authorization (RMA), and a ton more. The result? Greater efficiency and improved management practices across your entire company.
Contact us today to see how Brahmin Solutions can help automate your materials management.