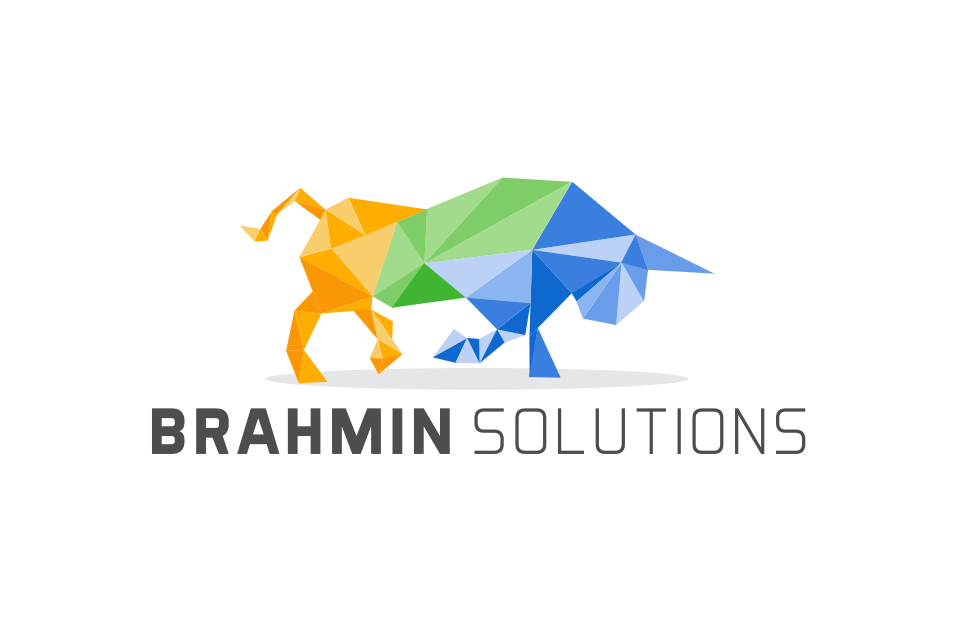
Manufacturing and Inventory Management Software
Have you ever heard of push and pull manufacturing? If you are a manufacturer, you have probably used one or a hybrid of the two methods.
The terms "push" and "pull" come from the supply chain management world. They are strategies used by businesses depending on the uncertainty of the demand for a product.
In push manufacturing, businesses produce products based on customer forecasted demands. This means that the companies make products even if the customers have not yet placed orders.
In pull manufacturing, production is based on customer orders. Once an order arrives, the work begins to create that product. There is no predicting or forecasting involved. In a pure pull system, no product is made until there is an actual order for it.
Those are the basic definitions, but there is much more to learn about both before deciding which is right for your company. Understanding the difference between a push system and a pull system is essential when it comes to managing product inventory as it is distributed to consumers.
Also, we will look at a third approach that combines the best parts of both, ensuring that inventory is appropriately distributed from the manufacturing facility to wholesalers and retailers, which can significantly reduce waste—a core principle of Lean Manufacturing.
Let's assume that you are a small beverage manufacturer that makes Kombucha:
If you were using the push manufacturing method, you would need to produce enough according to the demand forecast. This means figuring out how many units are usually sold and then adding in some extra units for safety stock.
Let's assume the forecast for the Kombucha manufacturer says they should produce 1000 bottles daily. This would lead to an extra 500 bottles in inventory until they are needed. When an order arrives, you would pull the necessary bottles from stock and ship them to the customer.
You are always maintaining an on hand of 500 bottles.
The best advantage of Push manufacturing — also known as make-to-stock (MTS) — is that it reduces the time between when an order arrives and when the customer receives the product.
With our Kombucha example, if a customer orders 100 bottles, the order can be filled immediately since we have the bottles on hand. This is a significant advantage for the customer because they don't have to wait for us to produce the desired product. Also, if there is an increase in demand, holding the extra inventory will allow the business to meet that demand instantly.
Push manufacturing can lead to high inventory costs. This happens when you pay your workers to produce 1000 bottles, even though you might only sell 500 daily. That extra 500 bottles sitting in inventory cost money.
Excess inventory takes up space, which could be used for other things, and it ties up capital that could be used elsewhere in the business.
If your company specializes in producing a single item or goods that take a long time to produce, then push manufacturing might be helpful for your business.
This type of manufacturing happens when the assembly line moves the product to the worker, instead of the worker going to the product.
An example of push manufacturing is Ford in the early 20th century. Ford used assembly lines and standardization to speed up production and reduce costs. This allowed them to push their product onto the market faster and more efficiently than ever before.
However, the Ford Model T was only sold in black from 1914 to 1925. This made it easier for Ford to sell their car because they only had to make one type. Without different models, there was no risk that Ford would have cars sitting around that people did not want to buy. But this also meant that people did not have a lot of choices when it came to what they wanted. Ford fixed this in 1926 by starting to sell different colors.
The rise of e-commerce is causing push-based supply chains and inventory management issues. It's difficult to predict customer demand with the sheer multitude of product variations. Let's take a look at the pull manufacturing process.
On the other hand, in the pull manufacturing method - also known as make-to-order (MTO) - you would produce only what the customer orders or what you sell on average daily. When a customer orders 50 bottles, your staff will produce just those 50 bottles specifically for that order.
The advantage of this manufacturing system is that you never have any inventory.
An example of a pull system is just-in-time manufacturing. The idea behind JIT is that the manufacturing process is scheduled so that the materials arrive at the facility exactly when production starts and production is scheduled so that it finishes just as the goods are dispatched to the customer.
Another popular approach to pull systems is Kanban. Kanbans are visual cues that tell you when to produce or get more of a product. For example, if there is only one item left with a Kanban on it and it's at the end of the supply chain, the Kanban will return to the start of the supply chain. That will tell you to produce more of that product. Another way to use Kanban is to have two product bins at the point of consumption or sale. When one bin gets empty, it will send a signal back to tell you to produce more so that the bin can be filled again.
One of the major disadvantages is that it can lengthen manufacturing lead times, for instance.
In our Kombucha example, if a customer orders 500 bottles, it will take them 10+ days for them to receive their product. That can be a big problem if the customer needs the bottles tomorrow.
Also, your workforce and production facilities can often be left idle in a pure pull system. It can also lead to massive delays if a supply chain issue arises and you can’t get the raw materials you need to produce your product.
The main difference between a push and pull system is that in a push system, the amount of product that reaches the market is based on how much production happens. But in a pull system, the amount of product produced is based on how much people are currently demanding. This fundamental difference in what triggers activities in the supply chain leads to different results for each system.
One major thing that sets push and pull systems apart is the amount of WIP inventory allowed. A pull system regulates the amount of WIP. In a push system, there is no definite limit on WIP inventory because no signals are coming back to the production floor.
Specifically, the WIP limit is reached when no products can be sold or consumed, i.e., there will be no signal that would trigger another replenishment. This means that at least one unit of product in WIP needs to be finished and sold before there can be another signal telling us to make more products.
The push system relies on forecasts to determine the production volume. But forecasts are never 100% accurate, so sometimes there will be too much or too little product. This can mean either inventory management resources and storage space taken up for no reason, or the product becomes "deadstock" and takes up resources for no reason.
A pull system only produces what customers have ordered. This way, there is always enough inventory and no waste. The only downside is that it might take longer for customers to get the product they want.
A push system is used to make sure customers always have the products they need. The push system makes sure that the products are available all the time. This is important in markets where lead times play an important role in customers' decision-making processes.
When a company offers its customers customization options, it would mostly do well to implement some features from a pull system in its production process. If not, they would need to build many different variants into stock, making it more complicated to produce them and taking up more space and money.
A pull system can help manufacturers keep their inventory down. A manufacturer can use a push system to stock up on products that don't need customization. Then, when the production process is required, a pull element will be used to get materials for that product. This is called a push-pull system.
There may be a way to use both push and pull methods to get both benefits.
In this system, you would have a small inventory to quickly cover unexpected spikes in demand and fill customer orders. But you would also produce items to stock the shelves based on historical data and customer trends. This way, you will not be caught unaware when your demand forecast predicts an uptick.
This hybrid push vs. pull manufacturing strategy could give you the best of both worlds: quickly filling orders and having products available when customers want them without having to keep a lot of inventory that may never sell.
Maintaining the right amount of materials and components to produce products can be challenging when you want to have a certain number of products available while also responding to customer demand which can change.
Maintaining (and training) an inventory management team that stays on top of that without the help of comprehensive software can become expensive.
That's where technology like Brahmin Solution comes in. This technology provides enterprise resource planning (ERP) and materials requirement planning (MRP).
To be agile and lean, you must coordinate all the moving parts of your manufacturing operation. This includes your supply chain system, sales and customer service, and everything else. You can see patterns and trends if you combine all the information about your customers, products, inventory, and suppliers. This will help you make adjustments to your production process as needed.
You can deliver the best of push manufacturing by having goods available when your customers want them. The most significant advantage of pull manufacturing is that manufacturers can leverage a pull system to reduce waste and maximize efficiency.
Moreover, you can do all this without relying on overworked (often error-prone) humans to track everything manually. That’s the power of a well-designed ERP system. Book a demo to learn more!