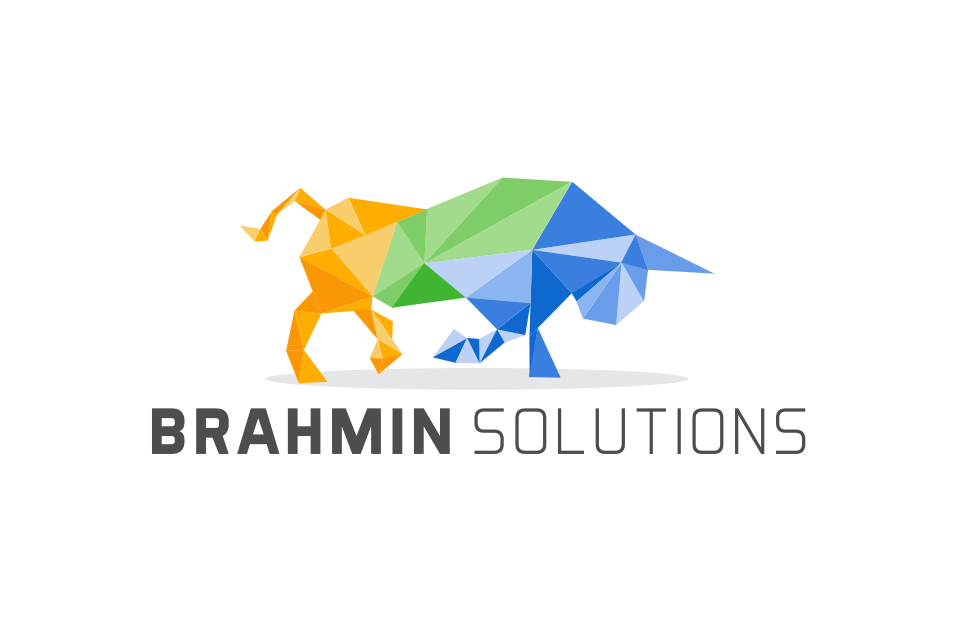
Manufacturing and Inventory Management Software
As a business manager, you know that your reputation is everything. Protecting your brand and building your customer base means providing a consistent, reliable, and, most importantly, high-quality product.
To do that, you need to have a solid grasp of quality assurance and quality control. Now you may think that whats the difference? Well lets break it down for you. We're going to cover both of these processes in detail. That way, you can start to strengthen both QA and QC at your business and build your brand.
Quality assurance, or QA, is the process of confirming that your business's quality requirements are being met. You should already have an idea in mind of the level of quality for your product. It's your goal post, a measurable way to track elements of your product that determine its quality.
Quality assurance is the strategies and processes you use to verify that your products meet that goal.
This is a forward-looking strategy used to maintain the quality of your products. In today's competitive market, your brand's reputation is undeniably linked to the quality of your products. When you maintain high standards, you not only meet but often exceed customer expectations. This cultivates trust and credibility, essential components for long-term customer loyalty.
High-quality products minimize returns and complaints, reducing the costs associated with customer service and refunds. This efficiency not only boosts your bottom line but also enhances customer satisfaction, creating a cycle of positive reviews and recommendations.
Ultimately, quality maintenance isn’t just about preventing negative outcomes; it's about proactive brand building. Invest in quality assurance and quality control practices to ensure your products meet the highest standards, and you'll foster a robust, positive brand reputation that stands the test of time.
You can think of it as being proactive and preventative. The goal is to get ahead of the quality of your products so that you can reduce the amount of time you spend correcting mistakes.
Another way of thinking about QA is that it builds quality into your products. This can substantially reduce the need to test and check the quality of your output.
Quality assurance (QA) practices vary significantly across industries, tailored to the unique requirements and standards of each field. However, the core objective remains the same: to ensure that the processes involved in production or service delivery consistently yield high-quality results.
In manufacturing, QA often involves rigorous process audits, ensuring that every step from raw material procurement to final product creation adheres to predefined standards. Techniques like Six Sigma and Total Quality Management (TQM) are commonly implemented to minimize variability and reduce defects.
Meanwhile, in the healthcare sector, QA is critical for patient safety and regulatory compliance. Here, methodologies might include regular clinical audits, staff training programs, and adherence to protocols set by bodies such as the Joint Commission or the ISO standards for healthcare services.
In information technology (IT), QA focuses on software development cycles. This entails rigorous testing phases, including unit tests, integration tests, and user acceptance tests, to identify and correct bugs early in the development process.
In the food service industry, QA involves ensuring that all food handling, preparation, and storage processes meet stringent health and safety regulations. Standards such as HACCP (Hazard Analysis and Critical Control Points) are employed to identify potential hazards and implement preventive measures to ensure food safety.
On the other hand, quality control is the process of checking that products have met your quality goals. It takes place after QA and the manufacturing process. It looks backward rather than forwards.
For example, during quality control (QC), you'll be inspecting and auditing products on various metrics. For the food industry, you could be checking for freshness and flavor. For glass manufacturing, you may be looking for air bubbles and durability.
Whatever sector you work in, quality control acts as a failsafe. It's how you ensure that your QA is working as it should.
With this in mind, it comes as no surprise that quality control is reactive and corrective. If QA is used to set you on the right path, QC is there to ensure you're staying on the right track.
When establishing your quality control strategy, you'll want to consider things like how often you check your products, how you correct a product that doesn't meet your metrics, and what metrics you're grading for in the first place.
When it comes to determining the frequency of checks, consider the nature of your product and the complexity of your manufacturing process. For example, high-risk industries like pharmaceuticals may need daily or even hourly inspections, whereas less critical products might only require weekly checks. Analyzing historical data on defects can also help pinpoint when errors are most likely to occur, allowing you to time your checks more effectively.
Effective corrective actions begin with identifying the root cause of defects. Utilize tools such as fishbone diagrams or the 5 Whys technique to dig deeper into why a problem exists rather than just addressing the surface issue. Once the root cause is identified, develop a step-by-step action plan to address the specific problem. This may involve adjusting manufacturing processes, offering additional training for staff, or sourcing higher-quality materials.
Regularly revisiting and updating your quality control strategy based on feedback and new data can also help maintain and improve product quality over time.
Now that we've covered the difference between quality assurance and quality control, it's time to discuss how you can manage both of these processes in your business. Below are specific practices you can embrace to ensure you're on the right track.
Since quality assurance is all about creating workable systems, make sure your training, planning, documentation, and monitoring are regularly updated. Since quality assurance is about proactive strategies, you're going to want to focus on the processes that go into developing and manufacturing your product. That means keeping your staff trained, your processes planned thoroughly, having plenty of documentation, and regularly updating your monitoring practices.
These are all factors you can set up ahead of time to ensure that your product is consistent.
Next, you should be updating these processes regularly. These are the processes that will be used to maintain your product quality, so they shouldn't go unchecked or unmonitored for any significant length of time.
As your product evolves, so should your QA practices. Keep your training relevant, planning on point, and read through and update your documentation as needed.
When keeping up with all of the various QA processes you've put in place, relying on a software solution can be helpful. You can use software like Brahmin Solutions to help you keep track of your inventory, production planning, and more.
It can also help you keep each of these components organized and automated. As mentioned, the goal of QA is to build quality into your products, and software is the perfect tool to help.
Since quality control is the more reactive approach, the first step it involves is identifying and remedying mistakes. This is where audits and testing come into play.
You should periodically check your products for defects, issues, and subpar output. Then, you should identify the cause of these issues and put the right teams on solving the problem.
Next, you'll need to define the testing procedures to perform quality control. That includes:
Keeping these processes updated and outlined will go a long way toward creating reliable QC measures. It'll also prevent oversight from your team because they'll know what to look for.
While quality assurance and quality control are separate processes, they can and should work together to help you reliably produce quality products. To do so, you'll need an approach as proactive as it is reactive.
That's where Brahmin Solutions comes in. Our experts have crafted software for manufacturers to build quality in mind. Reach our experts today to learn more.