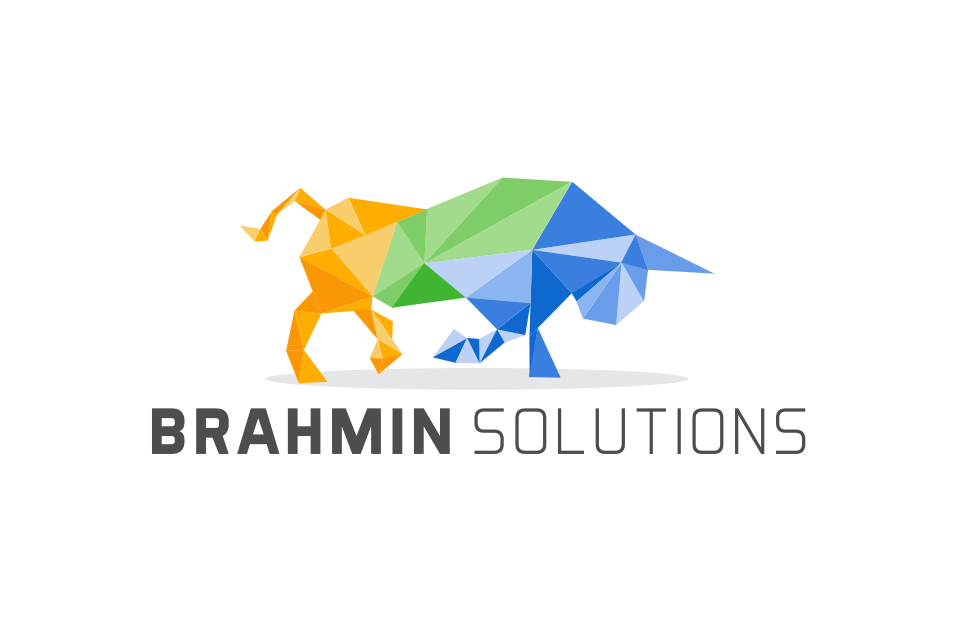
Manufacturing and Inventory Management Software
Order picking methods are an essential aspect of any warehouse. Compared to shipping, storage, and receiving, order picking is 50-60% of operating costs in a warehouse. Order picking efficiency correlates with how happy your customers are. If your picking methods are quick and accurate, your business will thrive and scale quickly. Here’s what you need to know about order picking and how and when to implement these best picking practices.
Order picking is the process of selecting items from a warehouse based on what the customer orders, this is a critical part of the supply chain and is considered the most labor-intensive and expensive activity for every business. As mentioned earlier, the cost of order picking is estimated to be as much as 50-60% of the warehouse operations. Since order picking is a costly process and can directly affect customer satisfaction, it is imperative that it be done efficiently and with little to no errors. Here are a few inventory management methods companies currently use:
The most common type of picking is a single order picking, this is found in smaller warehouses with low order volumes and a small number of SKUs. It is pen – paper method where orders are picked by an individual each time an order is placed. The picker must always make a full trip throughout the warehouse to pick one order. This method is inefficient. Warehouse management software can help solve this problem and increase productivity.
When to use it:
Total Orders – Low
Products Per Order – Moderate-High
Batch picking or multi-order picking as the name suggests picking orders in bulk. An order picker will pick all orders in a batch in one pass using a consolidated pick list. Usually, the picker uses a multi-tiered cart maintaining separate carton for each order or pick all the items and then sort at a packing station. Batch sizes typically run from 4 -12 orders per batch depending on the average picks per order. Since multiple orders are picked at once, it is essential that you have a system and procedures in place to prevent order mixing. To get maximum efficiency, batch orders, only when there is similar enough picks to create batches.
When to use it:
Total Orders – Low – High
Products Per Order – Low
Each zone has different pickers dedicated to that specific zone. These pickers are solely responsible for picking the orders from that zone. The retailer may receive an order from a different zone which can be picked by different employees and can be sorted at the packing station. This concept reduces warehouse travel time and increases the efficiency.
When to use it:
Total Orders – High
Products Per Order – Low-Moderate
Wave picking is a method in which the concept of batch and zone picking are applied together, all zones are picked at the same time and the items are later sorted to individual orders/shipments. Wave picking is the is usually the fastest method for picking multi item orders however the sorting and consolidation process can be tricky. Operations with high total number of SKUs and moderate to high picks per order may benefit from wave picking.
When to use it:
Total Orders – Low-High
Products Per Order – High